-
Products
-
IndustriesThe products are widely used in many industries, indluding shipbuilding, offshore engineering, petrochemical engineering, electric power, vehicle industry.
-
About UsTONGMING is one of the leading welding materials manufacturers in China. Since the inception of our operations in 2002, we have adhered to the highest standards of quality, research and innovation, and customer service.
-
NewsOur products have passed ISO9001 quality system certification, and have certified as high quality products by third parties from industries, such as nuclear power boiler and shipbuilding.
How To Choose The Right Grade For The Right Applications?
Apr 10,2024
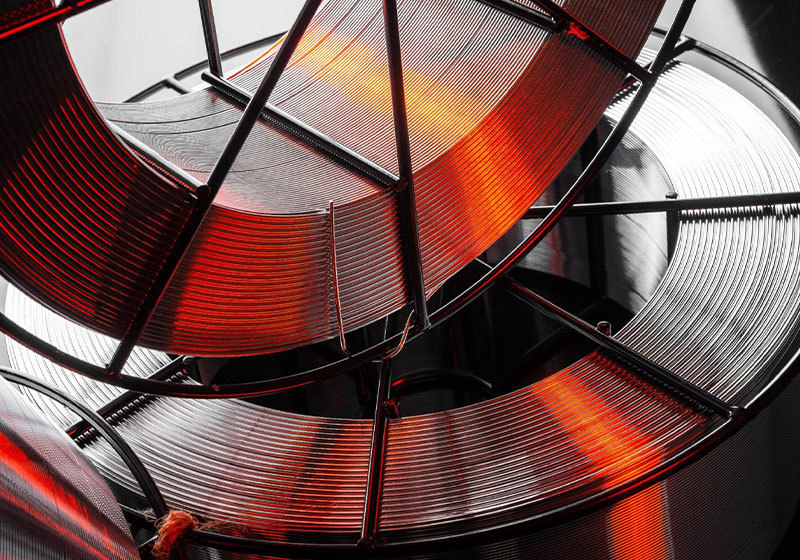
Stick welding requires practice to perfect, and choosing the right electrode for the job can be similarly difficult. Given the range of welding methods available, deciding which one is best for your shop can be a perplexing and tough decision. Choosing the appropriate welding rod might be difficult because there is no such thing as a universal electrode for welding in every situation. Since there is no one welding method, we need to evaluate the plus and minus points of all the welding procedures.
Weld Requirements
The first step is to determine what the weld will have to accomplish. What characteristics does it require? What type of metal are you utilising? Fill amount, position, speed of travel, and penetration are the four factors you will need to consider in any weld.
It’s considerably more crucial to have a fast-filling material in a heavy weld than it is in a tiny weld. If the weld isn’t horizontal, you’ll need a fast-setting weld. When working with thick metal, you’ll require a lot more penetration than when working with lighter metals, where burn-through can be a real issue. There are so many more factors that play a role in determining the ideal welding procedure such as the base metal being used, the efficiency of welders, the machine being used, filler wires being used, and so on.
Welding Procedures
★ The most frequently used welding procedures are MIG welding, flux-cored welding, gas tungsten arc welding (TIG welding), and shielded metal arc welding. There are some factors that we will need to consider before selecting one of the welding procedures –
★ The type of material that will be welded,
★ The material’s thickness,
★ The position of welding,
★ Power source for welding,
★ The quantity of current on hand,
★ Time requirements
Though most welding techniques may meet most of those requirements, you must first identify which process is ideal for the job. In general, each procedure has its own set of benefits and drawbacks.
MIG Welding
Metal inert gas welding, or MIG welding, is commonly used for big and thick materials. It employs a disposable wire that functions as both an electrode and a filler wire. It is substantially faster than TIG welding, resulting in shorter lead times and cheaper production costs.
Flux Cored Welding
Thicker metals are welded via flux core welding. It differs from flux core soldering in that the completed bond is significantly more secure, making it excellent for heavy-duty or industrial applications. When working on items like machine parts, this is critical. This flux core arc welding method is ideal for deep penetration of thicker metal pieces. However, it only works with mild and stainless steel, limiting your ability to use it on other metals in the future.
TIG Welding
Pipeline and pipe welding are the most common TIG weldingapplications. It is, nevertheless, employed in a variety of industries, including aviation and aerospace, as well as the sheet metal industry, when welding extremely thin materials and exotic materials like titanium. It does necessitate far more operator experience or training than other welding procedures, but it produces a precise, high-quality, and aesthetically pleasing weld.
Contact Us
E-mail :
wsn@hbtmhc.com
Phone/WhatsApp:
+86-13833932888
Address:
Qingliangjiang Industrial Park, Qinghe County, Xingtai City, Hebei Province

Export Manager: Ms. Wang
Qingliangjiang Industrial Park, Qinghe County, Xingtai City, Hebei Province
Request Quote