-
Products
-
IndustriesThe products are widely used in many industries, indluding shipbuilding, offshore engineering, petrochemical engineering, electric power, vehicle industry.
-
About UsTONGMING is one of the leading welding materials manufacturers in China. Since the inception of our operations in 2002, we have adhered to the highest standards of quality, research and innovation, and customer service.
-
NewsOur products have passed ISO9001 quality system certification, and have certified as high quality products by third parties from industries, such as nuclear power boiler and shipbuilding.
Do you know the properties and uses of cobalt-based welding rods?
Mar 26,2024
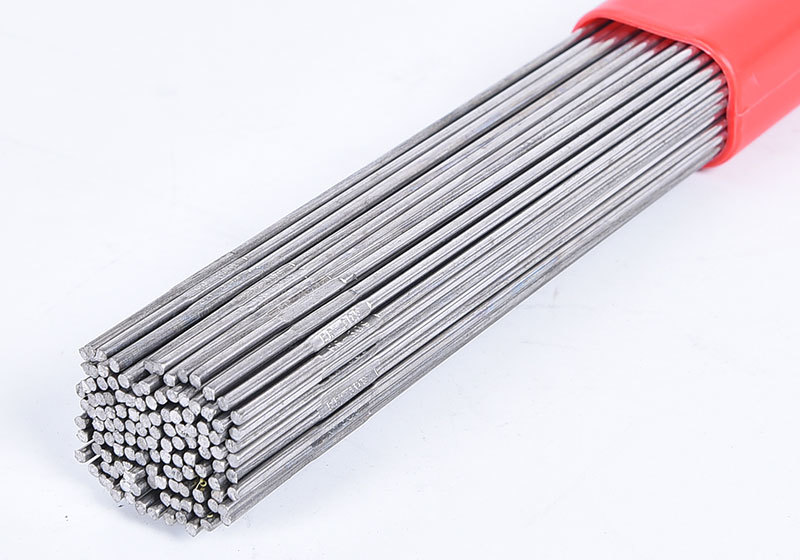
Cobalt-based welding rods have good comprehensive heat resistance, corrosion resistance and oxidation resistance, and can maintain high hardness at high temperatures above 600 degrees Celsius. Commonly used cobalt-based alloy surfacing deposits have oxidation resistance when they contain 25-33% chromium, and have high-temperature strength when they contain 3.0-14% tungsten. Cobalt is basically corrosion-resistant and belongs to a solid solution matrix. Carbon is an element. , which can improve welding.
When carbon and chromium combine to form hard carbides, the hardness of the deposited metal can be increased. As the carbon content increases, the hardness of the deposited metal increases and the toughness decreases to meet the needs of different uses. Deposited metal with low carbon content has good toughness and can withstand impact, corrosion and erosion under hot and cold conditions. It is suitable for surfacing welding of sealing surfaces of high temperature and high pressure valves, pump shafts, hot forging dies, hot shear blades, etc. and high carbon and high tungsten cladding.
At high temperatures of 540-650 degrees Celsius, alloy cobalt-based welding rods have good creep resistance and high-temperature hardness, which is the main reason why they are widely used in many occasions. Because there is more than 25% chromium in cobalt-based electrodes, a thin, tightly adherent and protective oxide scale can be formed under oxidizing conditions. In addition, alloy cobalt-based welding rods have good corrosion resistance in general corrosive media, so they are often used in working conditions that require wear resistance and corrosion resistance.
Although cobalt-based electrodes are widely used in wear resistance, if high temperature and corrosion are not important factors, then iron-based cladding electrodes can also obtain corresponding wear resistance. Cobalt-based electrode cladding uses DC reverse polarity. To prevent overlay welding, it should be preheated and cooled slowly. After the cobalt-based electrode is surfacing, it usually enters the welding state. However, it is generally recommended to carry out stress relief heat treatment for large-scale surfacing welding, and use nickel-chromium austenitic stainless steel as the transition layer for surfacing.
The use of cobalt-based welding rods
The cobalt-based welding rod with Cocrw core adopts DC reverse connection, and the cladding metal can still maintain good wear resistance and corrosion resistance at a temperature of 650 degrees Celsius.
Cobalt-based welding rod uses: 1. Used in places where good wear resistance and corrosion resistance can be maintained when working at around 650°C, or places where impact and alternating hot and cold conditions occur, such as cladding high-temperature and high-pressure valves and hot shear blades. 2. Used for shaft sleeves and lining sleeves of high-temperature and high-pressure valves, high-pressure pumps, cutting edges of chemical fiber equipment, etc. 3. Used for surfacing welding of wearing parts such as roller drill bit bearings, boiler rotating impellers, pulverizer cutting edges, screw feeders, etc.; 4. Used for surfacing welding of workpieces that withstand impact and alternating hot and cold conditions under high temperature conditions, such as Hot forging dies, valve sealing surfaces, etc. Good performance; 5. Used for high-temperature wear-resistant cladding electrodes, working temperature 1100, with red hardness and strong wear resistance. 6. It can also be used for hot section molds such as high-temperature and high-pressure valves, as well as components that are subject to impact, high temperature resistance, and corrosion resistance at the same time.
Contact Us
E-mail :
wsn@hbtmhc.com
Phone/WhatsApp:
+86-13833932888
Address:
Qingliangjiang Industrial Park, Qinghe County, Xingtai City, Hebei Province

Export Manager: Ms. Wang
Qingliangjiang Industrial Park, Qinghe County, Xingtai City, Hebei Province
Request Quote